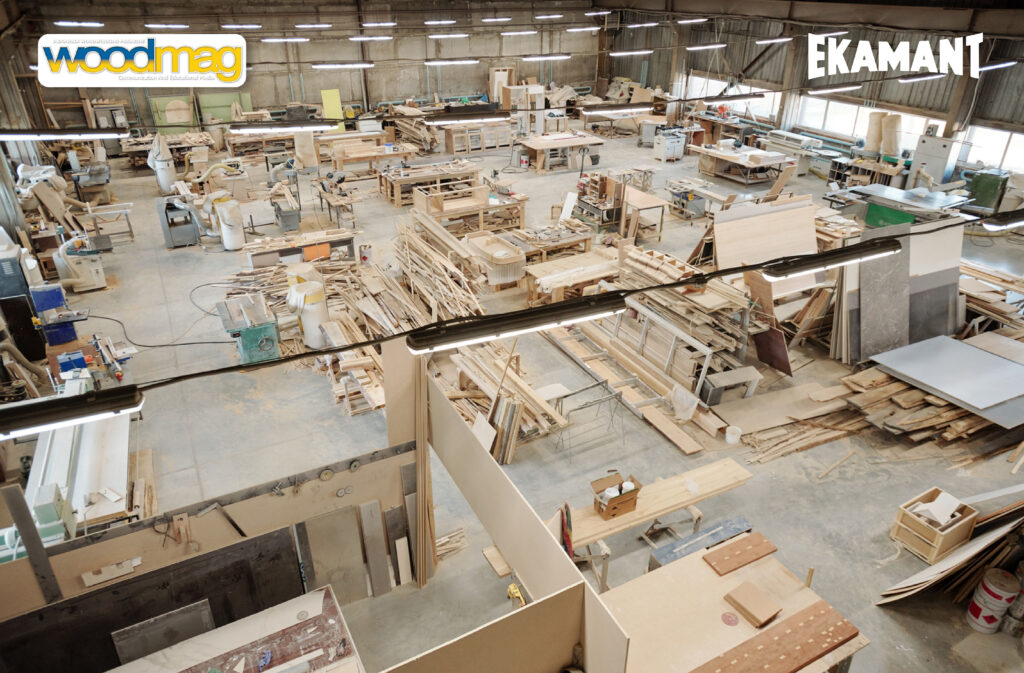
Konsep One Piece Flow adalah konsep aliran proses produksi. Dalam proses yang juga disebut dengan “1 piece aliran” ini, aliran proses produksi tidak ada hambatan dan stagnasi ketika prosesnya berlangsung. Hal ini sejalan dengan aktivitas menghilangkan salah satu waste yang dalam manufacturing yaitu bagian dari manajemen inventory.
Konsep One Piece Flow menjadi salah satu konsep yang ada di dalam metode Toyota Production System (TPS). Salah satu elemen penting dan paling dasar dalam konsep ini yaitu untuk menciptakan lingkungan yang ramping dan bisa beroperasi maksimal dengan aliran one-piece.
Terutama untuk proses produksi dari pabrik yang terbiasa dengan produksi barang secara batch. Untuk itu, bila alur kerja yang sudah sesuai Standar Operasional Prosedur (SOP) dipasangkan dengan teknologi yang tepat untuk mendukung proses produksi berlangsung, maka aliran One Piece Flow dapat menghasilkan manfaat yang signifikan dengan cepat.
One Piece Flow tidak hanya berbicara tentang cara kerja dalam manufaktur, tetapi juga berkaitan dengan aliran informasi dan aliran material yang disampaikan satu per satu tanpa adanya hambatan. Konsep ini akan menjamin dua hal tersebut berlangsung secara berurutan, ideal, dan menghindari potensi masalah yang mungkin terjadi.
Dengan menggunakan sistem conveyor, otomatis akan menghilangkan waste atau pemborosan yang terjadi di berbagai area, serta mampu meningkatkan efisiensi kerja. Buatlah proses kerja berlangsung secara mengalir, dengan informasi yang lancar tanpa hambatan.
Baca Juga: Kegiatan Training Ekamant Indonesia, Berbagi Ilmu untuk Customer
Ini bisa dilakukan secara bertahap dengan mengurutkan flow atau runtutan masing-masing proses kerja dan melihat apakah ada hambatan atau tidak. Selain itu, perhatikan juga kapasitas dan kecepatan masing-masing proses apakah sudah sama atau masih belum merata.
7 Keuntungan dari Implementasi Konsep One Piece Flow
Berikut adalah 7 keuntungan yang dapat diperoleh dari kesuksesan implementasi konsep One Piece Flow (OPF):
1. Memperbaiki kualitas dalam proses kerja
Produksi batch dengan jumlah massal memang bermanfaat dalam kasus-kasus tertentu. Namun, dengan produksi masif seperti ini tentu risiko cacat produk akan semakin tinggi jika terjadi kesalahan dalam prosesnya. Hal ini terjadi akibat ada lebih banyak stock barang yang perlu dipindahkan, dihitung, disimpan, dan diambil.
Dengan menggunakan konsep OPF, satu bagian yang cacat atau bermasalah secara kualitas hanya akan berdampak pada satu bagian saja. Oleh karena itu, Anda tak perlu mengerahkan pekerja atau operator untuk melakukan pemeriksaan ulang.
Sebaliknya, operator hanya perlu melacak alur kerja untuk satu bagian saja dan menentukan tindakan penyelesaian untuk memastikan masalah tidak akan terulang kembali.
2. Mengurangi stock atau inventory
Setiap operasi dalam proses produksi hanya perlu menghasilkan apa yang dibutuhkan oleh operator berikutnya. Dalam kata lain, hasil dalam proses A akan digunakan dalam proses B dan begitu seterusnya sampai proses akhir.
Ketika proses produksi diikuti dengan benar, sesuai SOP, dan memanfaatkan sistem produksi mengalir/conveyorsystem, maka proses ini akan menghilangkan peluang untuk terjadinya stock atau barang lebih yang tidak terpakai di tengah prosesnya.
3. Mengurangi pemakaian area kerja
Karena tingkat persediaan berkurang, maka akan lebih sedikit ruang dan tenaga kerja yang dibutuhkan untuk mengelola proses produksi mulai dari proses menerima, menghitung, menyimpan, memilih, dan mengirimkan barang.
OPF menghasilkan area kerja dengan tata letak yang dioptimalkan, sehingga satu operator dapat mengawasi banyak bagian selama berjalannya proses dengan lebih efektif dan efisien.
Baca Juga: Tips Menerapkan Metode 5S dalam Industri Woodworking
4. Meningkatkan fleksibilitas manufacturing secara keseluruhan
Lebih sedikit inventaris di yang berceceran di lantai akan memungkinkan waktu tunggu menurun. Mengapa demikian? Sebab, dengan inventory yang lebih rapi, dapat memberikan lebih banyak waktu dan fleksibilitas manufacturing, termasuk bagi tenaga kerja untuk mengurusi pesanan pelanggan. Dengan begitu, proses kerja akan menjadi lebih cepat, fleksibel, dan proses abnormal yang terjadi menjadi lebih mudah terlihat.
5. Mudah mengidentifikasi Kaizen
Jika proses abnormal berkurang dan persediaan stock Work in Process juga berkurang, maka masalah di lapangan akan semakin terlihat jelas. Ini akan mempermudah Anda untuk menyelesaikan masalah satu per satu yang menjadi hambatan dalam proses produksi dan perubahan akan lebih cepat terlihat hasilnya.
6. Menjamin lingkungan kerja yang lebih aman
Ketika stock atau inventory lebih sedikit, maka akan lebih sedikit juga masalah yang terjadi saat proses kerja berlangsung. Ini memungkinkan untuk memberikan peluang dalam meningkatkan tata letak peralatan di area kerja menjadi lebih baik dan lebih aman. Sehingga dapat pula mendeteksi potensi bahaya yang mungkin terjadi dengan baik.
7. Memperbaiki level moral karyawan
Dengan masalah terkait produksi yang dapat segera diatasi, area kerja menjadi lebih clear dan longgar, hal ini akan memberikan impresi kepada setiap karyawan untuk bekerja lebih giat dan bertanggung jawab dengan lebih baik.